Headquartered in Canada, Steel-Craft Door Products has been producing high-quality doors for residential, commercial and industrial customers since the company was founded in 1963. Though they don't manufacture their own garage-door openers, Steel-Craft is a leading distributor of LiftMaster brand door openers. Refresh the mesh back on your Raynor Ergohuman Chair with Replacement Mesh Backs for ME7ERG ME8ERGLO and LEM4ERG chair models. Available for sale at Human Solution now.
Raynor is a US manufacturer of residential garage doors made of steel and aluminum, as well as commercial sectional and rolling doors. The company established in 1944 is based in Dixon, Illinois.
On code.msdn.com there is a very useful WCF Binary message inspector extension for fiddler. W hat do we need to do to make this (very useful) extension work with the default 'REST with binary' encoding used by the WCF RIA Services release candidate? The RIA service breaking changes doc says this: Changed server communication from SOAP with binary encoding to REST with binary encoding. Wcf binaryencoded message inspector for fiddler for mac.
Products made by this brand can be particularly long-lasting, especially if they are installed by professionals and if you follow instructions from the Raynor garage door opener manual.
Yet there may be an issue at times. It is a smart idea to start by consulting the Raynor garage door troubleshooting chart below. When you have an understanding of the problem, you will be able to decide whether you really need someone’s help to finish Raynor garage door repair.
Raynor Premium series 8500RGD Prodigy II garage door opener troubleshooting
One of Rayonor’s most well-known Premium series models, the 8500RGD Prodigy II garage door operator may be used on both residential and light duty commercial doors. It was created exclusively for sectional doors with torsion assemblies. One of the convenient features available in this model is battery backup.Problems | Solutions/Symptom |
1 Flash Safety reversing sensors wire open (broken or disconnected) OR 2 FLASHES Safety reversing sensors wire shorted or black/white wire reversed | One or both of the Indicator lights on the safety sensors do not glow steady. • Inspect sensor wires for a short (staple in wire), correct wiring polarity (black/white wires reversed), broken or disconnected wires, replace/attach as needed. • Disconnect all wires from back of garage door opener. • Remove sensors from brackets and shorten sensor wires to 1 -2 ft. (30-60 cm) from back each of sensor. • Reattach sending eye to garage door opener using shortened wires. If sending eye indicator light glows steadily, attach the receiving eye. • Align sensors, if the indicator lights glow replace the wires for the sensors. If the sensor indicator lights do not light, replace the safety reversing sensors. |
3 Flashes Door control or wire shorted | The door doesn't activate from the door control. • Inspect door control/wires for a short (staple in wire), replace as needed. • Disconnect wires at door control, touch wires together. If garage door opener activates, replace door control. • If garage door opener does not activate, disconnect door control wires from garage door opener. Momentarily short across red and white terminals with jumper wire. If garage door opener activates, replace door control wires. |
4 Flashes Safety reversing sensors slightly misaligned (dim or flashing LED) | Sending indicator light glows steadily, receiving indicator light is dim or flashing. • Realign receiving eye sensor, clean lens and secure brackets. • Verify door track is firmly secured to wall and does not move. |
5 Flashes Motor RPM is not recognized | Door travels 2-3 inches and stops. • Reprogram limits and forces. • If the motor unit continues to travel 2-3 inches, check the travel module connection or replace the travel module.' SYMPTOM: No movement, motor runs 2-3 seconds. • Reconnect the emergency release. • Motor may need to be replaced. |
9 Flashes Cable tension monitor reversal | Door stops and reverses while closing. • Check for possible door obstructions and remove. • Check that the cable tension monitor is properly connected to the opener. • Replace the cable tension monitor. |
10 Flashes Limits and forces need reprogramming | Door stops while opening. • Reprogram limits and forces. |
11 Flashes Limits and forces need reprogramming | Door stops and reverses while closing. • Reprogram limits and forces. |
12 Flashes Attempting to compensate | Door stops and reverses while closing. • Garage door opener will try to compensate three times before turning to a 10 Flash. |
13 Flashes Attempting to compensate | Door stops while opening. • Garage door opener will try to compensate three times before turning to a 11 Flash. |
The garage door doesn't operate from the MyCF Home Control App or website. | • When using Model 580LG Alternate Power Supply or when in Battery Backup mode, the Internet Gateway will not activate the garage door through the MyQ® Home Control App. If you wish to use the Internet Gateway with your garage door opener, please contact your local electrician to wire an outlet next to the garage door opener. |
The garage door opener doesn't operate from either the Door Control or the remote control: | • Does the garage door opener have electric power? Plug a lamp into the outlet. If it doesn't light, check the fuse box or the circuit breaker. (Some outlets are controlled by a wall switch.) • Have you disabled all door locks? • Is there a build-up of ice or snow under the door? The door may be frozen to the ground. Remove any restriction. • The garage door spring may be broken. Have it replaced. • If the yellow command LED does not turn on, reverse the wires connected to the RED and WHT terminals of the control panel. Replace wire if necessary. |
The yellow and red LEDs on the Door Control are blinking quickly: | • The control panel is charging, and may take up to 5 minutes to become operational. |
My remote control will not activate the garage door: | • Verify the lock feature is not activated on the door control. • Reprogram the remote control. • If the remote control will still not activate the door check the diagnostic codes to ensure the garage door opener is working properly. |
The remote control has short range: | • Change the location of the remote control in your car. • Check to be sure the antenna on the side or back panel of the garage door opener extends fully downward. • Some installations may have shorter range due to a metal door, foil backed insulation, or metal garage siding. |
The door doesn't open completely: | • Check power door lock. • Is something obstructing the door? Is it out of balance, or are the springs broken? Remove the obstruction or repair the door. |
The door opens but won't close: | • Check cable tension monitor • If the garage door opener lights blink, check the safety reversing sensor. • If the garage door opener lights don’t blink and it is a new installation. For an existing installation. Repeat the safety reverse test after the adjustment is complete. |
The door reverses for no apparent reason and garage door opener lights don’t blink: | • Check cable tension monitor. • Is something obstructing the door? Pull the emergency release handle. Operate the door manually. If it is unbalanced or binding, call a trained door systems technician. |
Raynor MJ5011UCHB garage door opener troubleshooting
The MJ5011UCHB garage door opener produced by the US-based manufacturer Raynor is a medium duty door operator equipped with a built-in 315 MHz radio receiver. The model was created exclusively for commercial use. The opener system can perform not more than 12 cycles per hour or 50 cycles per day.Raynor Model 120 7 Manual Pdf
Condition | Possible cause | Fix |
Operator will not respond to any commands | A) No power | ― Verify primary line voltage (120 Vac, 60 Hz) is present at terminals L1 & 12. The LED will flash when power is present. |
B) Stop circuit not complete | ― Verify Stop Button input (terminals 3 & 5) is properly wired and stop button is not stuck. | |
C) Stuck button on 3-button control station | ― Verify that all buttons are actuating freely and releasing properly. | |
D) Interlock input activated | ― Verify jumper is located at terminals 3 & 4 if interlock is not present. | |
― Verify interlock is properly wired and not activated. | ||
E) Motor overload tripped | ― Overload is internal within motor. Allow to cool and retry. | |
F) Accessory failure | ― Attempt to close by holding the CLOSE button for more than 5 seconds. If door closes, check accessory for proper wiring, polarity, connections or damage. | |
― Verify photoelectric sensors are aligned or sensing edge is not activated. | ||
G) Possible component failure | ― Call Technical Support for assistance. | |
Operator makes noise but door does not move | A) Clutch slipping | ― Adjust clutch |
B) Brake not releasing (if present) | ― Verify brake assembly operation and wiring. | |
C) Door operation problem | ― Disconnect trolley and check door for proper operation. | |
Operator moves in the wrong direction | OPEN and CLOSE button wiring connection reversed | ― Check 3-button control wiring. |
Door drifts after operator stops | A) Door not balanced property | ― Disconnect trolley assembly and check door for proper operation. |
B) Clutch slipping | ― Adjust clutch | |
C) Brake not functioning properly | ― Check brake mechanism to ensure brake lever is free and brake pads are engaging the brake disc. | |
Door opens/closes too far | Limits not adjusted properly | ― Adjust limits. |
Door reverses unexpectedly | Intermittent Entrapment Protection Device activation | ― Check all connections. |
Ttc not functioning | A) Monitored Entrapment Protection Devices | ― Check all connections. Verify photoelectric sensors are not blocked and the sensing edge is not activated. |
B) TTC temporarily disabled | ― Close and Open the door. TTC will be re-enabled. | |
C) TTC not programmed properly | ― Reprogram TTC. | |
No response | A) Remote control is not programmed | ― Make PROGRAMMING REMOTE CONTROLS |
B) Remote control not compatible | ― Obtain qualified LiftMaster remote control device. | |
C) Low battery | ― Replace battery. | |
Remote cannot be learned | A) Low battery | ― Replace battery. |
B) Remote control not compatible | ― Obtain qualified LiftMaster remote control device. | |
Poor radio range | A) Low battery in remote | ― Replace battery. |
B) Antenna not configured | ― Configure the RADIO ANTENNA. | |
C) Ambient radio interference or building structural issue | ― Use EXTERNAL ANTENNA kit |
Raynor FliteStar-7 garage door opener troubleshooting
Raynor FliteStar-7 is a residential garage door opener created for up to seven foot high doors. The opener provides additional safety due to the auxiliary entrapment protection system complementing the usual built-in safety reverse feature. If the entrapment protection device is not installed, the door won’t operate correctly.Symptom | Probable solutions |
Operator runs from radio controls but not from push button | Check connections at push button and operator terminals. Wire may be broken under staples or at terminals. |
Reverse wires at terminals 6 and 7 on the back of the opener. | |
Remove wires from terminals 6 and 7, momentarily short across terminals 6 and 7, if operator runs then replace wall button. | |
Operator runs from push button but not from radio control | Check battery in transmitter. |
Check receiver and transmitter code setting. | |
Measure the voltage at terminals 1 and 3 on the 3 position terminal strip at the rear of the operator. With terminal 1 being negative and terminal 3 being positive, voltage should read between 20-28 VDC. | |
If it is necessary to return radio controls for repair, both transmitter and receiver must be returned. | |
Operator does not run from push button or radio control | Illuminated wall-mounted push button lock switch is activated. Operator plugged into outlet. |
Burned out fuse or open breaker. | |
Pull power plug and plug back in. | |
Replace microprocessor control board. | |
Operator stops functioning after repeated cycling | Motor may be overheated. Wait 20 minutes and try again. Replace microprocessor control board. |
Less than 25 feet operating range from radio control | Change battery in transmitter. |
Change location of transmitter in auto. | |
Mount receiver to wall and wire to operator. | |
If two or more operators are located within the same building, unplug all other operators and then test range. | |
Faulty radio - return to distributor to repair or replace | |
Motor hums but will not open or close the door | Jammed or hard moving door. Disconnect door from operator and check door for correct balance and operating condition. |
Do not disconnect an opened door, if door spring is broken the door may fall at a high speed and cause injury or property damage. | |
Repairs and adjustments, especially to cable and spring assembly, can be hazardous and should be performed by qualified door installers only. | |
Bad capacitor - Visually inspect capacitor | |
Motor - Disconnect motor leads and test motor windings and thermal protector with ohmmeter. Replace motor if windings or thermal protector are open. (Motor must be cool to test.) | |
Check for proper electrical connections. | |
NOTE: If operator is activated but does not open or close door, motor will shut off after approximately 25 seconds. | |
Unwanted (phantom operations) | Short in push button circuit. |
Check where stapled to wall or ceiling. | |
Check connections at both ends of the wire. | |
Can be caused by signal from another radio control in the area. Change frequency of radio control. | |
Door stops while it is opening | Make sure there is no obstruction keeping the door from opening or closing, either during door travel or photo eye obstruction. |
Door reverses while it is closing | Disconnect door arm and check door operation by hand. |
Adjust force adjustment sensitivity. Turning the screw counter-clockwise will require more force to stop or reverse the door. After making adjustments the safety reverse test must be performed. | |
Light will not come on | Check light bulbs and replace if burnt out. Check electrical connections. |
Faulty microprocessor board. | |
Illuminated wall-mounted push button locked. | |
Light will not go off | Press wall button or radio control to reactivate timer. |
Wait 5 minutes before initiating another signal. Light should go off. Faulty microprocessor board. | |
Door does not fully open or close | Make sure there is no obstruction keeping the door from opening or closing. |
Operator limit switch settings need adjustment. | |
Operator will not reverse when door hits an obstruction while closing | CAUTION - Do not use a door operator that does not reverse when coming in contact with a solid object 1 inch from the floor. If the operator cannot be made to function properly, disconnect and disable it until a qualified door installer can make repairs. |
Readjust force adjustment sensitivity. Turning the screw clockwise will require less force to reverse the door. | |
Close limit not set properly. Adjust close limit for more travel. | |
Radio control will only operate to open the door | External entrapment safety device malfunction check instructions for device used. Red light on back of operator will be on to indicate this. |
Wall button must be held in to close the door | External entrapment safety device is not installed. This is normal operation without device installed. |
Burned out fuse or open breaker | MOV on terminal strip blown. Remove cover and visually inspect MOV. (Power head Assembly, for location.) If discolored, deformed, or cracked, replace MOV. |
Raynor COMMANDER 2000RGD garage door opener troubleshooting
Raynor COMMANDER 2000RGD is a residential garage door opener powered by a 1/2 HP motor. It is important to point out that the door operator system won’t work correctly unless the protector system is properly aligned. The troubleshooting tips below will enable you to fix the garage door opener on your own in case of minor issues.Situation | Probable Cause & Solution |
The opener doesn 7 operate from either the door control or the remote control: | 1. Docs the opener have electric power? Plug a lamp into the outlet. If it doesn't light, check the fuse box or the circuit breaker. (Some outlets arc controlled by a wall switch.) |
2. Have you disabled all door locks? | |
3. Is there a build-up of ice or snow under the door? The door may be frozen to the ground. Remove any restriction. | |
4. The garage door spring may be broken. Have it rcplaccd. | |
5. Repeated operation may have tripped the overload protector in the motor. Wait 15 minutes. Try again. | |
Opener operates from the remote control, hut not from the door control: | 1. Is the door control push bar lit? If not, Remove the bell wire from the opener terminal screws. Short the red and white terminals by touching both terminals at the same time with a piccc of wire. If the opener runs, check for a faulty wire connection at the door control, a short under the staples, or a broken wire. |
2. Arc the wiring connections correct? Review Installation | |
The door operates from the door control, but not from the renwte control: | 1. Is the door push bar flashing? If your model has the Lock feature, turn it off. |
2. Your opener needs to re-lcam a remote control code. | |
3. Program the receiver to match the remote control code. | |
4. Repeat the rccciver programming procedure with all remote controls. | |
The remote control has short range: | 1. Change the location of the remote control in your car. |
2. Check to be sure the antenna on the right side panel of opener extends fully. | |
3. Some installations may have shorter range due to a metal door, foil backcd insulation, or metal garage siding. | |
Opener noise is disturbing in living quarters of home: | If operational noise is a problem bccause of proximity of the opener to the living quarters, the Vibration Isolator Kit 41A3263 can be installed. This kit was designed to minimize vibration to the house and is easy to install. |
The garage door opens and closes by itself: | 1. Be sure that all remote control push buttons and battery indicator lights arc oil'. |
2. Remove the bell wire from the door control terminals and operate from the remote control only. If this solves the problem, the door control is faulty (rcplace), or there is an intermittent short on the wire between the door control and the opener. | |
3. Clear memory and reprogram all remote controls. | |
The door doesn’t open completely: | 1. If the door has been working properly but now doesn't open all the way, increase the up force. |
2. Is something obstructing the door? Remove the obstruction or repair the door. | |
3. If door opens at least 5 feet, the travel limits may need to be increased. One turn equals 2 inches of travel. Repeat the safety reverse test after the adjustment is complete. | |
The door stops but doesn't close completely: | Review the travel limits adjustment procedures Repeat the safety reverse test after any adjustment of door arm length, close force or down limit. |
The door opens but won't close: | 1. If the opener lights blink, cheek the safety reversing sensor. |
2. If the opener lights do not blink and it is a new installation, check the down force. For an existing installation, sec below. Repeat the safety reverse test after the adjustment is complete. | |
The door reverses for no apparent reason and opener lights don't blink: | 1. Is something obstructing the door? Pull the manual release handle. Operate the door manually. If it is unbalanced or binding, call for professional garage door service. |
2. Clear any ice or snow from the garage floor area where the door closes. | |
3. Review the force adjustment procedures | |
4. If door reverses in the fully dosed position, dccrcasc the travel limits. Repeat the safety reverse test after adjustments to force or travel limits. The need for occasional adjustment of the force and limit settings is normal. Weather conditions in particular can affect door travel. | |
The door reverses for no apparent reason and opener lights blink for 5 seconds after reversing: | Check the safety reversing sensor. Remove any obstruction or align the receiving eye. |
The opener lights.. | Don't turn on: Rcplacc the light bulb(s) (100 watts maximum). Use a standard neck garage door opener bulb if regular bulb burns out. don't turn off: Is the Light feature ow? Turn it off. |
The opener strains or nuiximum force is needed to operate door: | The door may be out of balancc or the springs arc broken. C lose the door and use the manual release handle to disconnect the trolley. Open and close the door manually. A properly balanced door will stay in any point of travel while being supported entirely by its springs. If it docs not, disconnect the opener and call for professional garage door scrvicc. Do not increase the force to operate the opener. |
The opener motor hunts briefly, then won't work: | 1. The garage door springs arc broken. Sec above. |
2. If the problem occurs on the first operation of the opener, door mav be locked. Disable the door lock. Repeat the safety reverse test after the adjustment is complete. | |
The opener won't operate due to power failure: | 1. Use the manual release handle to disconnect the trolley. The door can be opened and elosed manually. When power is restored, press the Door Control push bar and trolley will automatically rcconncct (unless trolley is in lockout position.) |
2. The Outside Quick Release accessory (lor use on garages with no scrvicc door) disconnects the trolley from outside the garage in ease of power failure. |
There are a few times when you may need to find the serial and/or model number for your garage door. Garage door manufacturers place stickers on the doors, often in more than one place with all the pertinent information like serial and model numbers about that particular door.
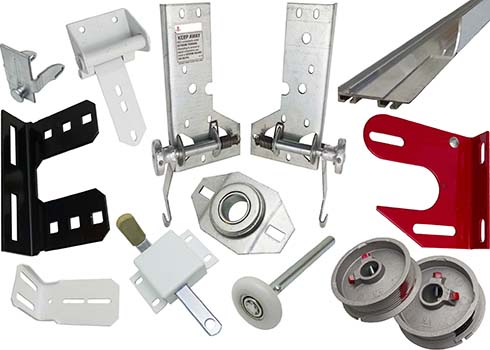
The stickers typically have the company name and logo on it. The stickers can be small or large.
Standing in your garage, facing the door (if it’s closed) look for the stickers on the interior surface of the door. A common placement for the sticker is in the lower left-hand or right-hand corner.
Here’s a picture of a Clopay sticker with serial number on it, located on the lower left-hand corner.
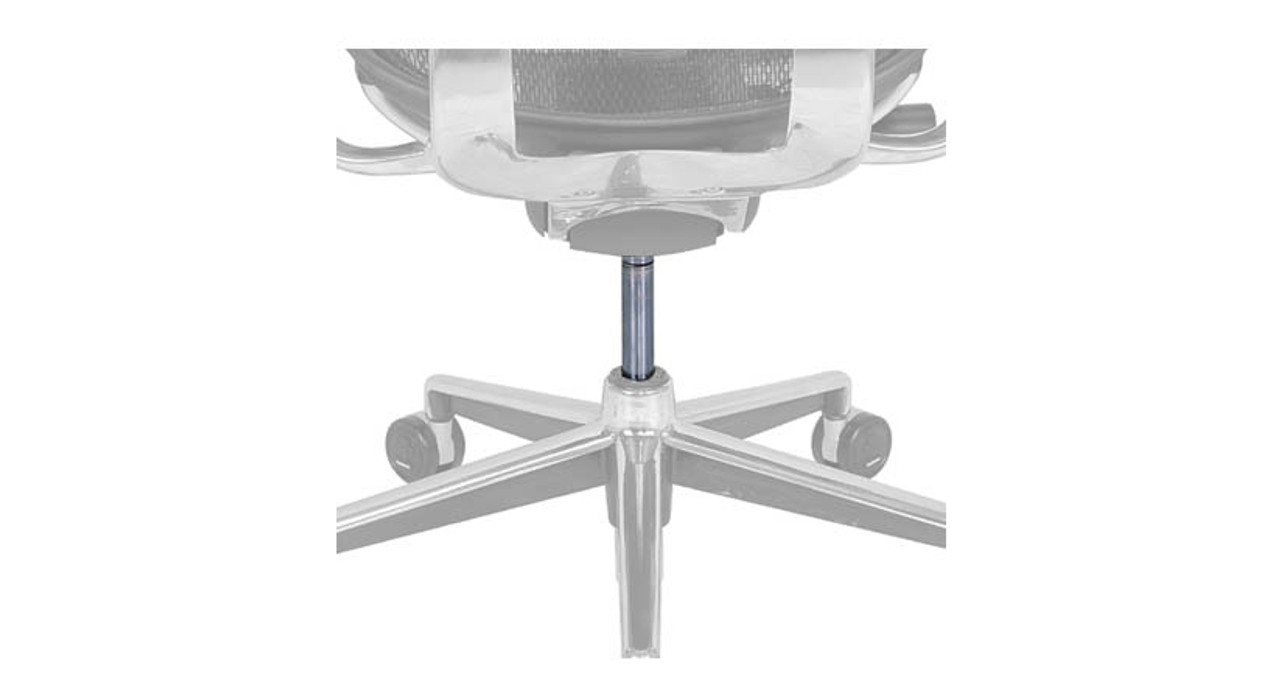
Close-up of the Clopay sticker:
Here’s an example of a larger sticker in the middle right-hand side of the door.
If you don’t see a sticker on the interior surface of the door, move to the side of the door and look up and down the height of the door for a narrow sticker. If your door is stuck in an open position, it may be harder to inspect this area.
Here’s a sticker on the side of the top panel of the door. You can see the Model Number 4050 on it (top row).

Garage door consists of panels. You may see a sticker on each panel of your garage door.
***NOTE***
Sometimes the stickers are peeled or ripped or torn off (picture below). If you don’t see a sticker or have a hard time finding the information give us a call 303.565.6409. Our technicians have installed thousands of doors and can help you with your garage door.
About the numbers:
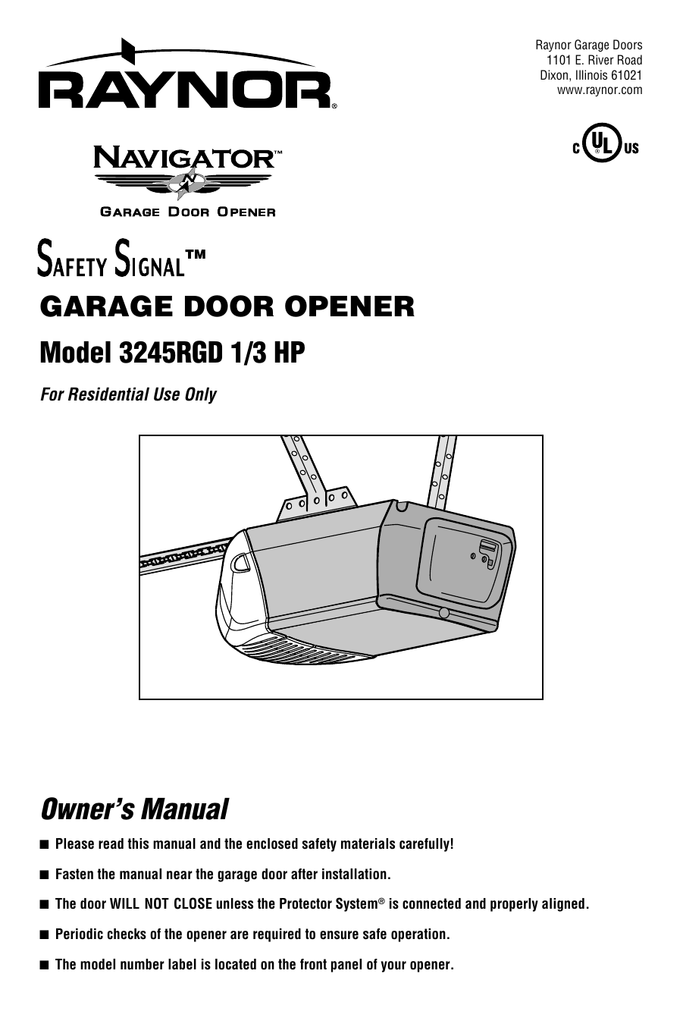
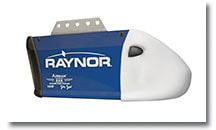
Model number or (PID) The summer i turned pretty pdf weebly free.
Model number specifies the model of the garage door you have, e.g. like in the photo above the Clopay door model number is 4050.
Serial Number
The serial number shows when your garage door was made, what batch of materials were used and other identifying information about your particular door.
Raynor 120-7 Manual
If you have any questions at all, give us a call 303.565.6409 we are here to help you with your garage door.
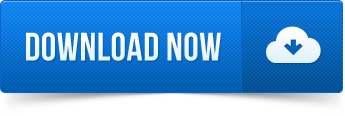